www.auto-innovations.net
26
'23
Written on Modified on
CUMMINS News
cummins SIMPLIFIED: THE TYPES OF TURBOCHARGERS
Cummins Inc. offers a range of turbochargers to support a wide variety of engine requirements used in countless applications.
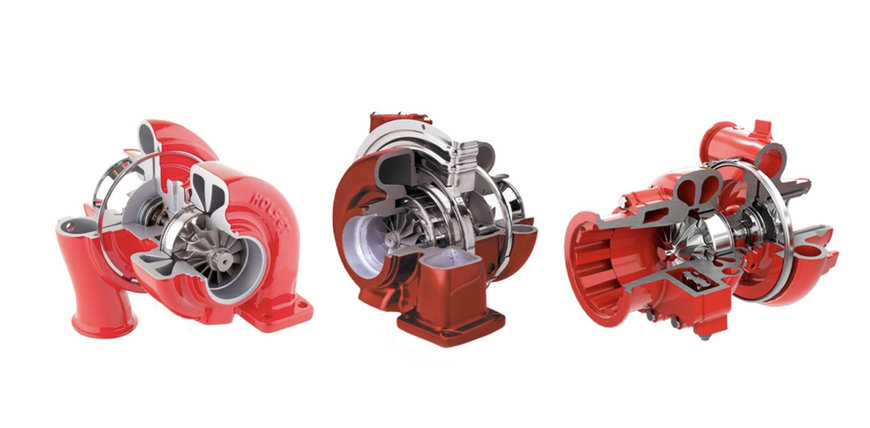
The primary types of turbochargers are Fixed Geometry Turbochargers, Wastegate Turbochargers and Variable Geometry Turbochargers. Engine manufactures consider several factors when choosing the type of turbocharger that is best for their engine and application. This article will help you understand the basic differences between these types of turbochargers. If you are interested, you can also read about how Cummins has found success in cold testing its turbochargers.
Turbochargers increase air flow to the engine cylinders, allowing for greater power density of the engine which improves combustion. Turbochargers use the energy in the engine exhaust gas to rotate a turbine at high speeds. A shaft connects the turbine wheel to a compressor wheel. The rotating compressor increases the pressure and flow of fresh air to the engine.
The differences between the types of turbochargers described in this article are based on how the exhaust gas is manipulated before it reaches the turbine wheel.
Fixed Geometry Turbochargers
The exhaust gas flows through the turbocharger turbine housing before reaching the turbine wheel. A cavity in the turbine housing is called the volute. With Fixed Geometry Turbochargers, 100% of the exhaust gas flows through the volute to the turbine wheel.
The wheel of the turbine and the shape of the volute affect the turbocharger and the engine performance. The turbine housing and wheel geometries are designed to optimize performance across various engine speeds and loads. Some Fixed Geometry Turbochargers also include a nozzle with fixed vanes to improve turbine performance at specific operating conditions.
The advantages of Fixed Geometry Turbochargers, compared to the other designs, are the simplicity of the design, low cost and smaller size. The main disadvantage is the lack of flexibility in optimizing engine performance. Given its fixed geometry, compromises must be made between optimal engine transient response, peak torque capability, and engine rated speed and power.
Fixed Geometry Turbochargers are often used in engines that operate at a constant engine speed. This includes engines used in power generation and large industrial and marine applications. Fixed geometry turbochargers are rarely used in on-highway applications.
Wastegate Turbochargers
A Wastegate Turbocharger is similar to a Fixed Geometry Turbocharger with an added feature in the turbine housing: a wastegate valve. When the valve is open, a portion of the exhaust gas by-passes the turbine wheel and reduces its speed. This helps regulate airflow from the compressor to the engine. With Wastegate Turbochargers, a smaller turbine housing can be selected to increase air flow to the engine at low engine speeds. This improves engine response and vehicle acceleration. The wastegate valve is then opened at higher engine speeds to prevent over boosting the engine and to prevent the turbocharger from exceeding its rotational speed limit.
Compared to Fixed Geometry Turbochargers, a big benefit for Wastegate Turbochargers is that they offer more flexibility in optimizing engine performance. One of the challenges is that Wastegate turbochargers are slightly more expensive and are larger in size due to the addition of an actuator (a component that produces force or torque) to operate the wastegate valve. Actuators may be either pneumatic (mechanical) or electric.
Wastegate Turbochargers are primarily used in applications that operate at varying engine speeds and loads. These engines are used in a variety on-highway and off-highway applications.
Variable Geometry Turbochargers
Variable Geometry Turbochargers are more complex than Fixed Geometry and Wastegate Turbochargers. Variable Geometry Turbochargers work by varying the area of the exhaust passage immediately before the exhaust gas enters the turbine wheel. Reducing the area increases the pressure and the velocity of the exhaust gas entering the turbine wheel. This in turn increases boost pressure and air flow to the engine when desired. Heady-duty trucks that operate in diverse environments with varying loads can be a great example where the benefits of the Variable Geometry Turbocharger can help.
Variable Geometry Turbochargers can be more expensive than other types of turbochargers. While they are expensive, Variable Geometry Turbochargers do offer the benefit of significant optimization of engine performance across a wide range of engine speeds and loads. These turbochargers can also be used to enhance engine braking, drive exhaust gas recirculation and support exhaust aftertreatment thermal management. Cummins patented Holset VGTTMcontinues to deliver superior turbocharger performance and durability in commercial applications.
Variable Geometry Turbochargers are used on a wide variety of applications to help meet the most stringent emissions regulations. They are primarily found in on-highway and off-highway applications with varying engine speeds and loads because they help ensure optimized performance across many applications and duty cycles.
Engine manufacturers consider various trade-offs when choosing turbochargers and air handling architectures. Some engines use a single turbocharger while others use more than one turbocharger arranged in a series or in parallel configurations.
www.cummins.com